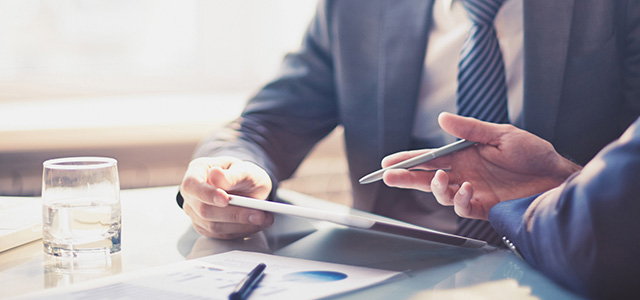
自卸车车厢制造工艺及工装
工艺及工装设计说明
一、焊接主线
1、 料区:主要存储框架式车型框架用料,料台采用框架结构,承重不小于10吨,最长工件为8.5m,最短工件0.8m,来料加工采用天车,送料采用天车或人工。
2、 底架拼焊:工件尺寸:8.5m*2.5m,重量2吨;工件向前反装,分别以下平面、纵梁、后端梁和一侧边梁为基准准确定位,总装配关联件符合图样要求,采用气动夹紧,拼焊完成后,滚动道升起,人工将工件推至下一工位。
3、
底架焊合(左):工件尺寸和重量同上,工件向前反装,工作台可侧翻90º,工件与输送轨道分离,使焊接部位处于水平状态且固定牢靠。侧翻系统采用液压装置,能在与水平夹角90º范围内任意位置可靠定位,工件处于90º位置时,最低点应高于地平面150mm,工件至水平位置时应停放在输送轨道上,由人工送至下一工位。
4、 底架焊合(右):同上。
5、
底板拼焊:工件尺寸:8.5m*2.5m,重量3吨;该工位设置半门吊1台,移动16米,垮度7米,起重量2吨,提升高度4m,用于底板和底架上位。工件向前反装,采用可移动式上压紧装置,夹紧位置应满足自工件边缘起1250处,夹紧点应满足工艺要求;拼焊完成后,输送轨道升起,人力输送到下一工位。
6、 底板总成焊接:工件尺寸:8.5m*2.5m,重量3吨,工件向前反装,工件上平面为基准平面,以后端梁和纵梁为平面位置定位基准,设翻转座套、油缸(三角臂)等总装配关联件定位装置。焊接及辅架装配完成后,输送轨道升起,人力将工件输送到下一工位。
7、 校正清理:工件尺寸及重量同上。工件停放在输送轨道上,工装设多点液压装置,采用火焰法对工件进行校正。完成后,输送到翻转工位。
8、 翻转焊接:工件尺寸同上。工件向前反装,停靠在输送轨道上,纵向定位,链式翻转机启动可将工件可靠定位于任意位置,使焊接位置处于水平状态,工件内容完成后,由人力将工件输送到下一位置。
9、
厢体拼焊:工件尺寸:8.5m*2.5m,重量6吨。工件向前正装固定在轨道上,以底板前端和左侧边双向定位夹紧;立体定位夹紧台架保证前板和左侧板与底板相对位置;厢体随行定位夹具保证右侧板和底板、前板及左侧板的相对位置;定位台架应与工件吊装物移动及相关焊机附属装置不发生干涉。拼焊完成后,工件由人力送到下一工位,工位设门式吊车一台,起重量2吨垮度9米,提升高度6米,吊钩移至房柱6米,用与前板侧板就位。
10、
合厢焊接1:工件尺寸:8.5m*2.5m*2m,最大重量6吨,工件向前正装至固定式输送轨道,纵横双向定位。工装:①前侧板内外立缝焊接自动小车,外侧为固定悼导轨式,内侧为电磁导向移动式,两套同时自上向下施焊。②两侧板内侧与底板采用移动导轨式自动焊接小车,自工件后端向前端施焊(外部人工施焊同时进形),焊接内容简介完成后,厢体内焊接工装上移,工件由人工推到下一工位。
11、 合厢焊接2:工件尺寸和重量同上。工件向前正装至固定输送轨道上,纵横双向定位。该工位主要是人工补焊完成上工位各焊缝,含前板与底板内外焊合;同时将侧板内外加固板与厢体拼焊牢固,完成后解除定位,人工利用输送轨道送至下一工位。
12、 厢体焊接3:工件尺寸与重量通商。工件向前正装于输送轨道,纵横双向定位,人工对内外侧的加强板施焊,也可以采用厢体焊接1类似工装实施纵向自动焊接,完成后推至下一工位。
13、 厢体焊接4:工件尺寸和中重量同上。安装方式同上,由人工对外侧加固板与底板连接部分按图样要求施焊,以及相关联附件焊接。
14、 后板焊装及清理:工件尺寸及重量同上。工位设起重机一台,对横移过来的后板实施配焊。
15、 下线存放:完成后的确工件由10吨天车移至存放工位台架上,等待进入涂装工序。共设5台存放共位。
二、焊接辅线
1、副车架焊装线;
① 料区: 主要为纵梁件和加固板件,来料送料均为天车。
② 左右纵梁的的焊接:工件长为8.5米,槽形件。工装基本尺寸9*2米,两侧各为9*0.75米的焊接平台,中间宽0.5米为共用固定输送辊道。用于纵梁前后加固板的焊接,翻转轴套采用销轴定位完成后人工利用中间辊道送至下一工位。
③ 左右纵梁校正:工装基本形式——工件至于固定输送辊道上,液压缸侧向加压,加压支架纵向移动对弯曲部位实施矫正。完成后利用辊道送至下一共位。
④ 副车架拼焊:工装上平面为基准平面,以纵梁后横梁为平面位置定位基准,按图样要求对各类相关件实施定位夹紧。输送辊道为升降式,拼焊完成后辊道升起由人工送至下一工位。
⑤ 翻转焊接:工装的基本形式和要求:整体360°旋转,可在任意位置停止并自锁;两端纵向通过工件,工件支撑部分与工件输入辊道可人工分离输送辊道与上下工位输送辊道贯通,工件夹持可靠与人工旋焊不发生干涉。
⑥ 校正清理:工装为液压为液压动力上压式矫正装置,压头在工装 基面内可任意移动;升降式输送辊道应保证工件与工装上平面间隙不小于50mm。矫正完成后工件由人工送至下一工位。
⑦ 连接件焊接:工装上平面为基准平面,根据图样要求设置定位夹紧装置,完成翻转轴套油缸支架等总装关联件的焊接,同时视不同主机完成副车架与底盘车架连接件的焊装。
⑧ 存放:工件由天车下线至存放区等待进入涂装工序。
2、侧板焊装线(左右各一条)
① 共用料区:存放板料件尺寸8.5*1.5米,重约1吨,压形件最大重量为150公斤,来料由天车吊运,送料由门式电磁电车完成。
② 拼焊:工件尺寸8.5*1.5米,重1吨。工装上平面为基准平面,零件位置定位点按图样要求设置,工件正装,上边梁置工装外侧,采取旋臂上压式夹紧装置。自动焊接应按保证2台自动化小车各自在纵横两个方向施焊,且必须有定位锁紧装置。
③ 焊接:工件尺寸及重量同上。工件正装,工件上平面为基准平面,设升降输送滚道
④ 翻转焊接:工件尺寸及重量同上。工装整体360°旋转,可在任意位置停止并自锁;两端纵向通过工件,工件支撑部分与输送轨道可人工分离;输送轨道与上下工位输送轨道贯通;工作夹持应可靠;整体结构与人工施焊不发生干涉。
⑤ 校正清理:工件尺寸和重量同上。工装为液压动力上压式校正装置,压头在工件尺寸范围内可任意移动且实施校正功能,工件传送由升降式辊道实现。辊道升起位置应保证工件与工装上平面间隙不小于50mm.